Research
The world’s first metal 3D printer for space is on its way to the ISS
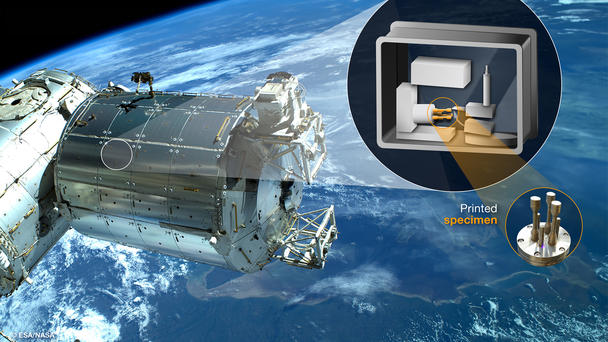
Soon, tests of the first metal 3D printer for space will take place on the International Space Station (ISS) Columbus module, which was created by Airbus* for the European Space Agency (ESA). It might significantly alter the course of manufacturing in space and upcoming lunar or martian missions.
The industrial process known as Additive Manufacturing (AM) has given rise to new perspectives on part design. It can be used for a wide range of tasks, from routine maintenance to creating bio-ink implants, from building spacecraft parts to printing entire homes.
The International Space Station (ISS) currently has multiple plastic 3D printers; the first one was delivered in 2014. Because obtaining equipment can take months, astronauts have already used them to replace or repair plastic parts. This is because one of the main challenges of living in space is the lack of supplies. However, not all materials can be made of plastic.
Over the next few decades, this logistical constraint will become more severe on future Moon and Mars stations. Printing the part is still more efficient than shipping the entire thing to its destination, even if the raw material still needs to be launched.
The second difficulty is safety: shielding the International Space Station (ISS) from the laser’s harsh printing environment and the heat it produces. Like a safe, the printer is housed in a metal box that is sealed. Significant thermal control is implied by the melting point of metal alloys that are compatible with this process, which can be far higher than 1,200°C compared to about 200°C for plastic.
Does metal printing work well in a microgravity setting?
One of the questions the team is attempting to address is this one. For this experiment, two printers will be used: an engineering model on Earth and a “flight model” inside the International Space Station. Four samples that the astronauts print in space will be returned to Earth for examination. The engineering model printer will be used to produce the same specimens. Girault adds, “ESA and Danish Technical University will conduct mechanical strength and bending tests as well as microstructural analysis on the parts made in space and compare them to the other specimens in order to evaluate the effects of microgravity.”
The quality of metal printing in orbit will be better understood due to metal 3D printing on board the International Space Station (ISS). It will also offer important insights into how to run a metal 3D printer in space. One major step towards preparing the technologies humanity will need for a long-term presence on the Moon is the printing of structural parts in space.
Research
Boeing’s Eco Demonstrator and NASA Investigate Sustainable Aviation Fuel Benefits
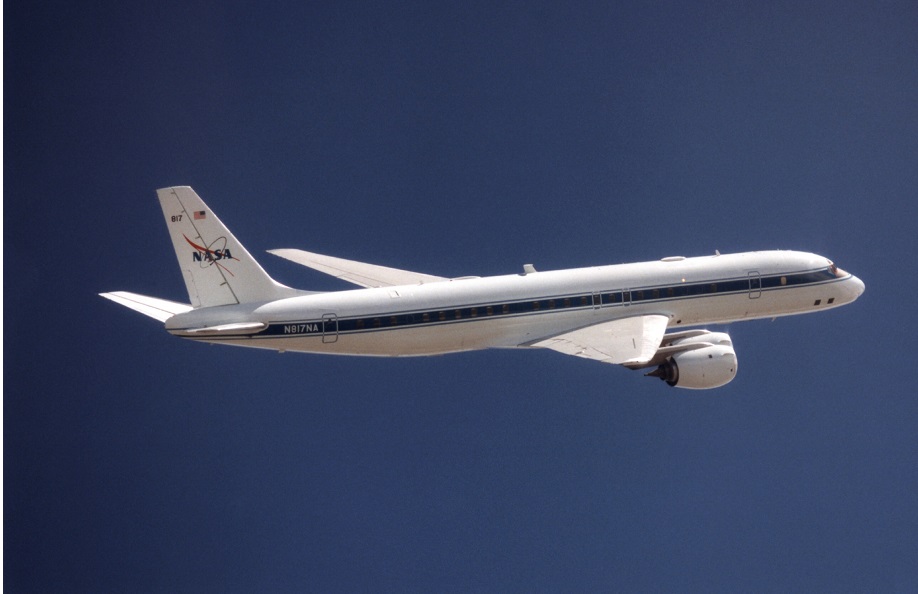
Boeing, NASA, and United Airlines will conduct tests to understand the benefits of sustainable aviation fuel (SAF) during air-to-air flights.
Boeing’s ecoDemonstrator Explorer, a United Airlines 737-10, will fly with SAF and traditional jet fuel separately. NASA’s DC-8 Airborne Science Lab will follow and measure emissions and contrail ice particles. They want to see how SAF affects contrails and if it reduces atmospheric warming.
The tests are supported by the FAA, GE Aerospace, the German Aerospace Center (DLR), and World Energy. World Energy will supply SAF from California.
This project is part of Boeing and NASA‘s ongoing partnership to study SAF’s impact on emissions. SAF can cut emissions by up to 85% compared to regular jet fuel and improve air quality near airports.
Boeing’s Chief Sustainability Officer, Chris Raymond, is hopeful about the project. NASA’s Rich Wahls believes flight testing is crucial for understanding SAF’s effects. United’s Chief Sustainability Officer, Lauren Riley, is excited about the potential of SAF. GE Aerospace is proud to support the research. DLR’s Markus Fischer sees this as an important step in reducing aviation’s climate impact.
Boeing’s ecoDemonstrator program aims to have 100% SAF-compatible commercial planes by 2030.
Aerospace
GKN and Pratt & Whitney collaborate to develop EWIS for hybrid demonstrator
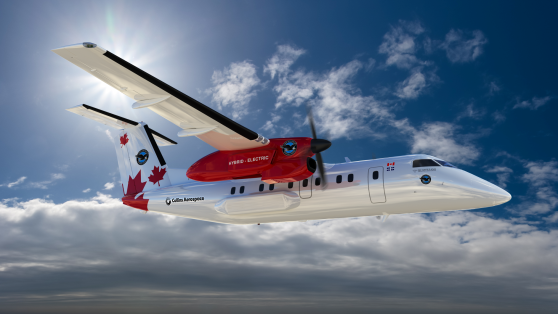
Pratt & Whitney Canada and GKN Aerospace have a contract in place to work together on the creation of the High Voltage High Power EWIS for the RTX hybrid-electric flight demonstration project. The demonstrator, which aims to have a 30% increase in fuel efficiency and a reduction in CO2 emissions compared to the most modern regional turboprop aircraft currently in use, will also have its electrical wiring system developed, built, and installed as part of the arrangement.
The hybrid-electric propulsion system of the demonstrator combines a fuel-burning engine from Pratt & Whitney with a 1-megawatt electric motor created by Collins Aerospace. More effective engine performance will be possible during the various flying phases, including takeoff, climb, and cruise, through the hybrid-electric system. Business divisions of RTX include Collins Aerospace and Pratt & Whitney.
The development and design of the High Voltage High Power EWIS for the hybrid-electric propulsion system will be led by GKN Aerospace in the Netherlands. After the design process, GKN Aerospace will be in charge of producing the required hardware and mounting it on the demonstrator aircraft.
Modern electrical distribution systems that are powering a substantial portion of today’s passenger flights and military aircraft are provided by GKN Aerospace, a renowned leader in engine systems and EWIS solutions for aircraft. Teams from all over the world, including Montreal, Canada, where the hybrid-electric flight demonstrator project is situated, provide assistance for GKN Aerospace’s EWIS centre of competence in the Netherlands.
Aerospace
S-92 Helicopter: A Journey from Ocean Rescues to Sustainable Aviation Fuel Innovation
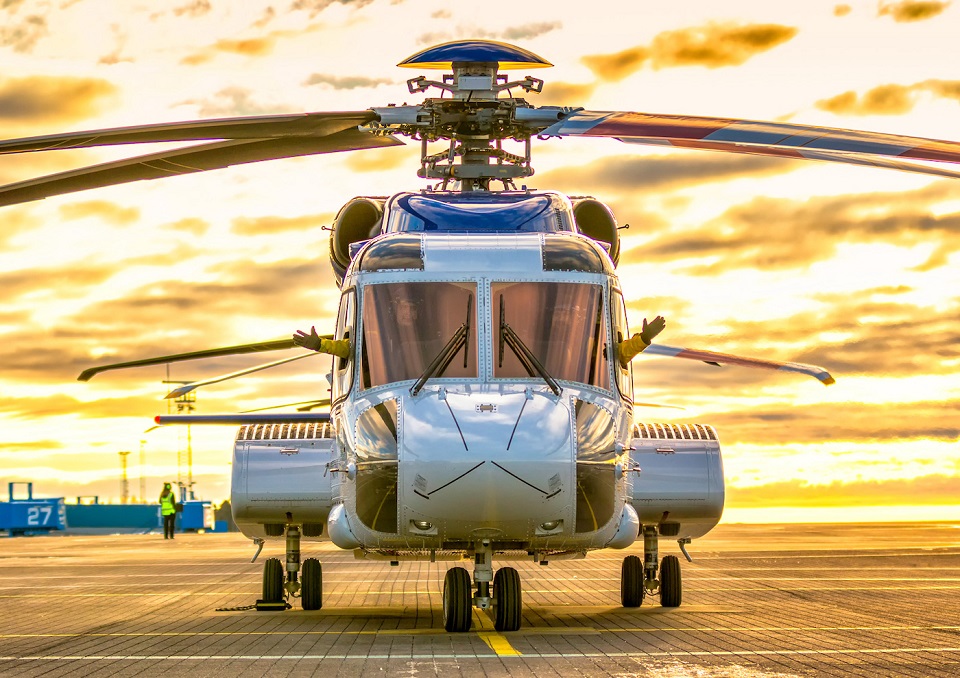
In 2019, a Sikorsky S-92 helicopter was dispatched to the rescue after the cruise ship Viking Sky made a mayday call. Crews managed to rescue 479 stranded tourists off the troubled liner before it limped back to the port despite 25-foot waves and howling winds.
This workhorse helicopter seems to be capable of almost anything: S-92s transport oil workers to offshore rigs, assist in border enforcement, and will soon transport the American president aboard Marine One. Even a booster rocket falling from space was caught in the air by an S-92 in 2021.
Two CT7-8A turboshaft engines from GE Aerospace, one of a class of engines that have accumulated more than 100 million flight hours since its introduction in the late 1970s, are powering this versatile helicopter.
As part of their maintenance, repair, and overhaul (MRO) at ITP Aero, a Spanish company that also services CT7 engines for Leonardo’s AW189/AW149 and the S-92, CT7 engines will now operate on a mixture of sustainable aviation fuel (SAF) and conventional jet fuel. The recently announced effort intends to further integrate SAF into commercial aircraft operations while reducing CO2 emissions at ITP’s site.
When it comes to CT7 engine maintenance, GE Aerospace and ITP Aero are taking the initiative to employ a SAF blend as they both work towards a lower-carbon future in which there may be an energy transition for helicopters and aeroplanes. SAF can be produced from a range of materials, including biomass, algae, fats, greases, and even collected CO2 and hydrogen. A standard for 100% SAF is currently being developed, however all CT7 engines, a development of the T700, can now run on a mixture of up to 50% SAF and normal aviation fuel.
One of the CT7’s selling points has always been its ease of maintenance. A CT7 that requires maintenance is taken to a specialised facility, like the ITP Aero facility in Albacete, Spain, which was first settled by Moors on the banks of the Don Juan River in La Mancha. Any engine that is put back into operation must undergo testing and qualification procedures.
-
Aerospace7 months ago
First Glimpse of Hungary’s KC-390 Aircraft by Embraer
-
Aerospace7 months ago
VoltAero Performs the World’s First Flight of an Electric-Hybrid Aircraft
-
Aerospace7 months ago
The Art and Science of Crafting Airbus A350 Wings
-
Aerospace7 months ago
S-92 Helicopter: A Journey from Ocean Rescues to Sustainable Aviation Fuel Innovation
-
Aerospace7 months ago
Airbus partners with DG Fuels to foster sustainable aviation fuel production in the United States
-
Aerospace7 months ago
GKN and Pratt & Whitney collaborate to develop EWIS for hybrid demonstrator
-
Uncategorized5 months ago
Difference between NASA and Space-x
-
Research5 months ago
Boeing’s Eco Demonstrator and NASA Investigate Sustainable Aviation Fuel Benefits